|
|
|
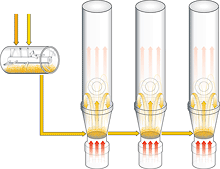 |
Semi-continuous wet granulation. In the mixer granulator.
Batch-by-batch drying. In the multi-chamber fluid bed dryer.
Flexible throughputs. Small sub-batches. Time-controlled,
continuous operation.
Consistent product quality. Exactly reproducible process steps.
Contained process. No cross-contamination.
|
|
|
|
Process advantages
Semi-continuous granulation is a combination of the division of a master
batch into exactly defined sub-batches, which sequentially pass through the
process steps of wet granulation in the mixer granulator, and subsequent drying
in the multi-chamber fluid bed dryer. Operation with defined and reproducible
sub-batches of constant quantity allows widely differing quantities to be
produced continuously.
VG wet granulation is an important technology for the manufacture of
granules, pellets and tablets. Granules from vertical granulators (also forced,
moist or wet blenders) are distinguished by a compact structure with good flow
characteristics, as the product is mechanically compressed during the
process.
|
|
|
Principle of operation
The starting product is accurately dosed and thus divided into sub-batches.
These are wet granulated in the mixer granulator. Due to the patented design of
the mixing tool, the product is completely transported into the following drying
chambers. This gives uninterrupted continuous operation of the granulator
over a long period without shutdowns for cleaning. The wet granule is sieved
by means of a fast-acting sieve between the mixer granulator and the first fluid
bed dryer.
|
|
Glatt Multicell GMC 30, Computer-monitored, fully automatic,
semi-continuous granulation line |
|
The wet granules are dried as sub-batches in the subsequent multi-chamber fluid
bed dryer. The product is automatically conveyed pneumatically from one chamber
to the next and out of the last tower into a separator. The finished granule is
poured into a container via a dry sieve.
|
|
|